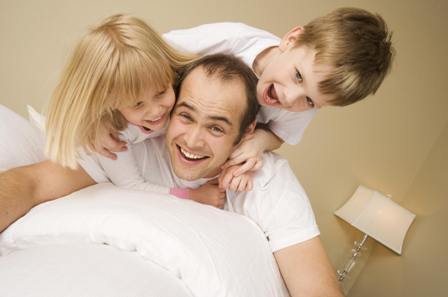
10 бальнеологических курортов Карпат
Карпатские бальнеологические курорты – это источник здоровья и жизненной энергии. С помощью лечения минеральными водами можно избавиться от многочисленных заболеваний и поддержать общий тонус организма. Благодаря комплексу оздоровительных процедур, включающему питьевые минеральные воды, живительные ванны и грязи, из организма выводятся токсины и шлаки, исчезает синдром хронической усталости, нормализуется давление. Не случайно чудодейственные свойства бальнеотерапии ценили еще древние греки, а вы можете убедиться в ее эффективности на одном из многочисленных Карпатских курортов, наслаждаясь хрустальным горным воздухом и чудесными пейзажами. Предлагаем ознакомиться с рядом популярных курортов Львовщины…
ПРОГРАММА АВТОБУСНОГО ТУРА В КАРПАТЫ "ФАЙНЫЕ КАРПАТЫ"
1 День
19:30 - Сбор группы и посадка в городе Киеве (ст. метро Житомирская).
19:45 - выезд из г. Киев. (по дороге делаем остановки по 15-20 минут на каждые 2,5-3 часа следования по маршруту).