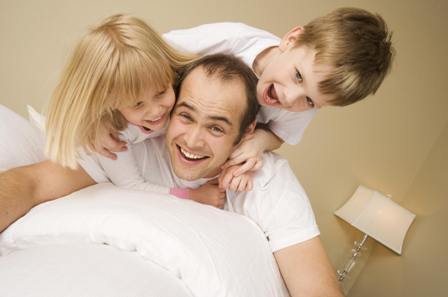
Берегово – закарпатский Эдем
Термальные воды, ароматные вина, прекрасная природа – колоритный закарпатский городок Берегово просто создан для оздоровительного и расслабленного отдыха. Расположенный в 5 километрах от венгерской границы, термальный курорт сохраняет настоящий европейский дух в благородной атмосфере города, стильной архитектуре, языковых традициях. Здесь даже время европейское. Местные жители, как и 500 лет назад называют свой город на венгерский манер Берегсас, а названия улиц пишутся на двух языках – венгерском и украинском. Берегово круглый год гостеприимно принимает желающих погрузить утомленные тела в целебные воды термальных бассейнов и предлагает отдыхающим…
Сбор группы и посадка в городе Киеве (ст. метро Житомирская). Посадкой в автобус занимается руководитель группы, который укажет Ваши места в автобусе и ответит на все Ваши вопросы при посадке. Контакты руководителя, марка и гос.номер автобуса будут указаны в инфолисте, который будет доступен за два дня до выезда в рубрике инфолисты.