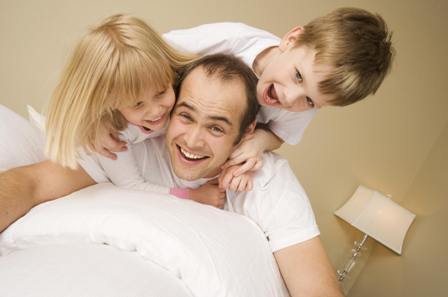
Тустань – «чи велетнів се, чи розбійників дім»
Эти строки Иван Франко посвятил в свое время древнерусской крепости-граду на фантастических Урицких скалах, которая вошла в летопись в качестве важного оборонного и таможенного центра Киевской Руси, а позднее и Галицко-Волынского княжества. Тустань в наше время – государственный историко-культурный заповедник, популярная туристическая жемчужина, визитная карточка карпатского исторического ландшафта.
Черновицкий университет – шедевр архитектуры эпохи Габсбургов
Назвать бывшую Резиденцию митрополитов Буковины и Далмации архитектурной жемчужиной как-то не поворачивается язык – это прозвучит чересчур банально. Даже эпитеты роскошная, изысканная, утонченная как-то бледно характеризуют украшение Черновцов. Она – грандиозна! Это подтвердит самый опытный знаток архитектуры. Таких идеальных архитектурных ансамблей на территории страны совсем немного, его уникальность подтверждена включением в реестр мирового наследия ЮНЕСКО, его непостижимая в своей монументальности красота покоряет с первого взгляда.