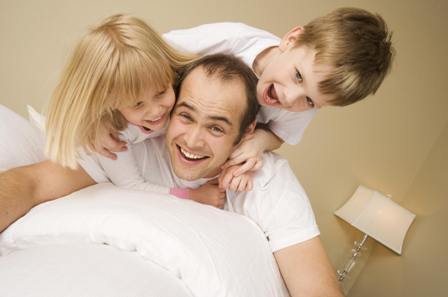
Охотничий замок Шенборна – украшение Закарпатья
Утонченный силуэт дворца Шенборна со стройными готическими башнями в урочище Берегвар выплывает из изумрудных лесных зарослей, словно сказочный мираж. Элегантное, неоренессансное сооружение, возведенное неподалеку села Карпаты Мукачевского района Закарпатской области, выглядит, словно благородная дама, заблудившаяся в диких карпатских лесах. Дворцу присуща некая отчужденность от всего земного вопреки вполне тривиальному назначению- уже более 60 лет в нем размещается центральный корпус санатория «Карпаты».
«Туманный» тур по достопримечательностям Львовщины
Ноябрь. Месяц пронзительного предчувствия зимы, когда стихает буйство природных красок, влажная опавшая листва с легкой, прощальной грустью шелестит под ногами, небо теряет свою глубокую синеву, и все чаще ложатся туманы. Плотный и тревожный туман сопровождал наше путешествие вместе с «Відвідай» по историческим достопримечательностям Львовщины, придавая поездке магического ореола, вызывая стойкие ассоциации с седой стариной.