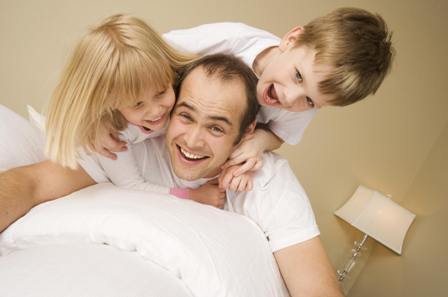
Катруся і Ксеня: новорічна казка
Початок грудня, вечоріє… За вікном львівський туман і дощ, ні сонечко не визирне, ні сніжок не припорошить землю. А всім так уже хочеться свята! Катруся кладе на підвіконня лист Миколаю, – може хоч цей добрий дідусь принесе новорічний настрій і маленького даруночка. Раптом з кімнати кличе мама: «А йди-но глянь, Катрусю!». На екрані комп’ютера неймовірної краси замок. «Ксенія» – читає вголос Катруся. Й одразу захоплено: «Що це?»
По дороге: остановка на Яблунецком перевале, высота которого – 931 метр над уровнем моря. Яблунецкий перевал образует границу, которая разделяет Закарпатскую и Ивано-Франковскую области. Фото-сессия возле самого большого деревянного герба Украины, посещение сувенирного рынка.