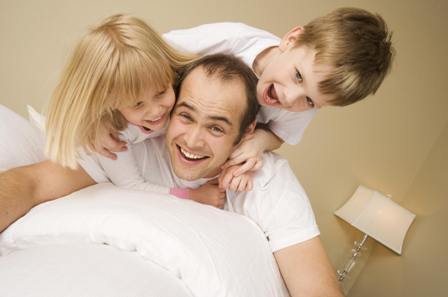
туры выходного дня в Карпаты
- Возвращение в с. Ясиня
- Ужин.
- Свободное время (по желанию: баня, сауна, чаны, колыба)
Школьные туры: 10 типичных ошибок организаторов
Наши менеджеры сформировали не один десяток туров для детей и проехали тысячи километров в качестве гидов школьных групп. Сегодня мы хотим поделиться с Вами перечнем типичнейших ошибок, допускаемых представителями школ, организаторами туров и родителями, планирующими путешествия для своих детей. Узнайте, чего не следует допускать, планируя школьные туры.