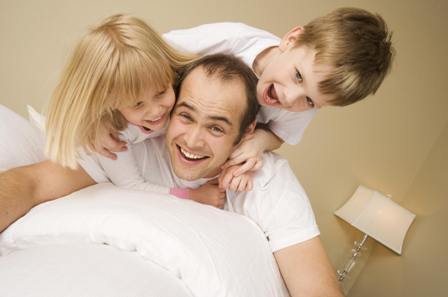
21 красивейший водопад украинских Карпат
В Карпатах есть много живописных уголков, где природа подтверждает, что она самый лучший художник. Одними из таких мест являются водопады. Предлагаем Вашему вниманию подборку самых больших, красивых, полноводных, а также сложно доступных водопадов Карпат. Одиннадцать водопадов находятся в Ивано-Франковской области (из них – шесть в массиве Горганы, в частности, в Надворнянском районе). Закарпатье в нашем списке представлено пятью водопадами, в частности, самым большим однокаскадным водопадом в Карпатах – Ялинским, высотой 26 м. Четыре из описанных водопадов располагаются на территории Львовской области и один – Черновицкой.…
10 бальнеологических курортов Карпат
Карпатские бальнеологические курорты – это источник здоровья и жизненной энергии. С помощью лечения минеральными водами можно избавиться от многочисленных заболеваний и поддержать общий тонус организма. Благодаря комплексу оздоровительных процедур, включающему питьевые минеральные воды, живительные ванны и грязи, из организма выводятся токсины и шлаки, исчезает синдром хронической усталости, нормализуется давление. Не случайно чудодейственные свойства бальнеотерапии ценили еще древние греки, а вы можете убедиться в ее эффективности на одном из многочисленных Карпатских курортов, наслаждаясь хрустальным горным воздухом и чудесными пейзажами. Предлагаем ознакомиться с рядом популярных курортов Львовщины…