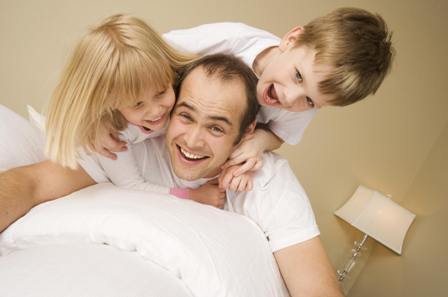
Кульчицы – родина гетмана Сагайдачного
Туристов всегда привлекают зрелища. Величественные замки, нарядные храмы, могучие скалы, да еще и с вереницей легенд в придачу – дух захватывает! Казалось бы, какую конкуренцию известным туристическим монстрам в лучшем понимании этого слова может составить маленькое, неприметное село? А между тем, любое, даже самое малоизвестное село Львовщины – живая легенда, поражающая своим мощным историческим наследием. И село Кульчицы Самборского района Львовщины – яркий пример того, как под верхним пасторальным природным слоем кроется, словно старинная фреска, эпичное полотно богатого исторического прошлого. Стоит только копнуть. Археологические находки,…
Ніхто не попереджав, що буде так! Або просто «Жидачівський Люрд + долина диких тюльпанів»
Чого я очікувала, виходячи з дому? Сама не знаю. Так вже сформувалося в моїй свідомості, що тур чи екскурсія, яка триває один день — це щось дуже неправильне, таке, що немає права на існування, адже поїздка обмежена в часі, всього лиш один день. Що можна встигнути за один день? Це ж настільки мало, навіть не встигаєш вбуватися, прожитися атмосферою самої екскурсії. Тому, мабуть, нічого особливого й не чекала. Але…